Ever wondered how the tiny parts in our modern world are made? The THY Precision injection moulding process step by step is key to understanding these tiny marvels. THY Precision, a top name in the field, will take you on a journey into plastic injection technology. They’ll show how it’s used in making micro-parts.
The injection moulding process step by step is crucial in making our world. It turns raw plastic into many different products with complex shapes. First, plastic pellets are melted. Then, they’re injected into special moulds. Finally, they cool down to become solid products.
This Injection Moulding Process Step by Step method is great for making lots of complex items. It uses special steel moulds to create parts with high precision and design. This process is key in the plastic industry for making detailed items.
Key Takeaways
- Understand the Injection Moulding Process Step by Step, from melting raw materials to solidifying final products
- Explore how plastic injection technology can be tailored for the manufacturing of micro-parts
- Discover the role of precision-engineered moulds and the importance of material selection in micro-parts production
- Learn about the benefits of Injection Moulding Process Step by Step plastic injection moulding, including superior surface finish, minimal waste, and tight tolerances
- Gain insights into the latest advancements in automation for enhanced precision and consistency in micro-parts manufacturing
Mastering the Injection Moulding Process Step by Step
At THY Precision, we know the details of the injection moulding process step by step. This method is key for making tiny parts with high precision. Let’s explore the main steps of this process.
Plasticizing: Melting the Raw Materials
The injection moulding process step by step starts with plasticizing. Here, we use medical-grade plastic pellets like Polypropylene (PP) at specific melting temperatures. Our top-notch machines make sure these materials melt fully and evenly, ready for the next steps.
Injecting the Molten Plastic
After plasticizing, we inject the molten plastic into a special mould. At THY Precision, we set our machines to meet the exact needs of each tiny part. This helps avoid mistakes and unwanted marks.
By getting these early steps right, THY Precision makes top-quality micro-parts. We ensure your products are reliable and perform well.
“The injection moulding process step by step is a symphony of precision, where each note must be perfectly in tune to create a masterpiece.”
Optimizing Mold Design for Micro-Parts
Getting the shape right is key for micro-part manufacturing. This means making a mold just for the part’s design. It’s important to tweak the injectionmoulding process step by step to get it right. This helps avoid problems like parts not fitting right or having rough edges.
The mold design is crucial for making sure the final product looks just like it’s supposed to. This is especially true for medical products. Precision engineering helps make molds that can create tiny parts with great accuracy and consistency.
To make the best molds for micro-part manufacturing, think about these tips:
- Use advanced tools to simulate how the melt will flow and fill the mold properly.
- Choose high-precision methods like micro-milling to make the mold with very small errors.
- Add cooling channels and other features to help the mold cool down quickly and evenly.
- Put in sensors and monitoring systems to keep an eye on the mold’s performance and make adjustments as needed.
By carefully designing and making the mold, THY Precision can make micro-parts that are perfect for medical, electronics, and other precise industries.
Mold Design Considerations | Key Benefits |
---|---|
Advanced Simulation and Analysis | Optimized melt flow and cavity filling |
High-Precision Machining | Tight tolerances for intricate micro-features |
Cooling System Design | Dimensional stability and rapid cycle times |
Integrated Monitoring | Consistent process control and quality assurance |
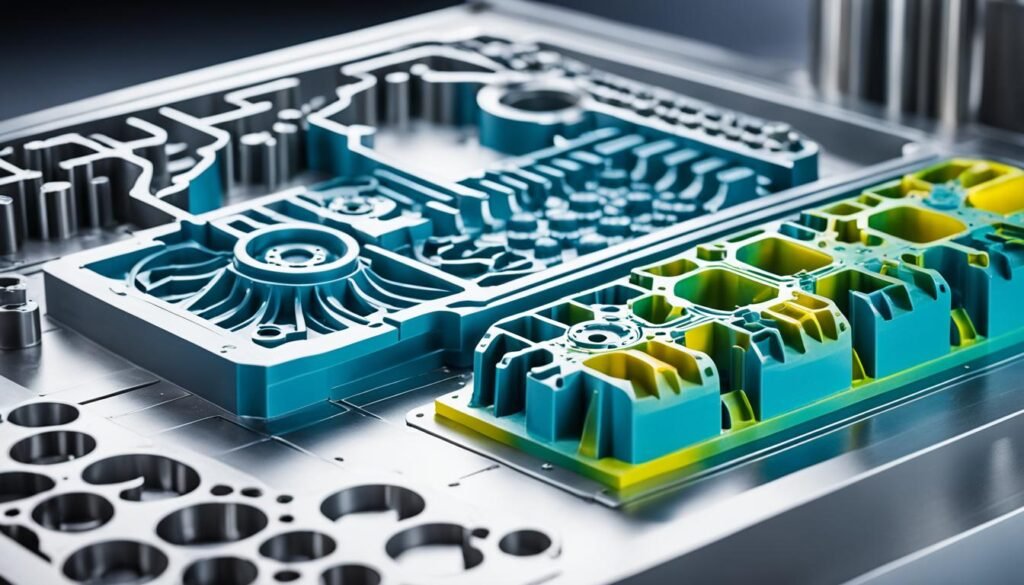
“Precision in mold design is the foundation for producing high-quality micro-parts that meet the most demanding specifications.”
Material Selection: Exploring Resin Options
In the world of injection moulding, picking the right resin is key, especially for micro-molding. THY Precision leads in injection moulding solutions, focusing on material properties for high-performance micro-parts. The choices you make can greatly affect the final product’s performance.
Resin Properties for Micro-Molding
For micro-molding, choosing the right resin is crucial. THY Precision’s experts look closely at viscosity, flowability, shrinkage, and thermal stability. This ensures the best resin for your micro-parts. We guide you through the process, helping you pick medical-grade plastics or specialized resins for the best results.
Producing intricate parts like optical components, electronics housings, or medical devices requires careful resin selection. With THY Precision, you can fully benefit from micro-molding. Our expertise helps you get the material properties and quality you need.
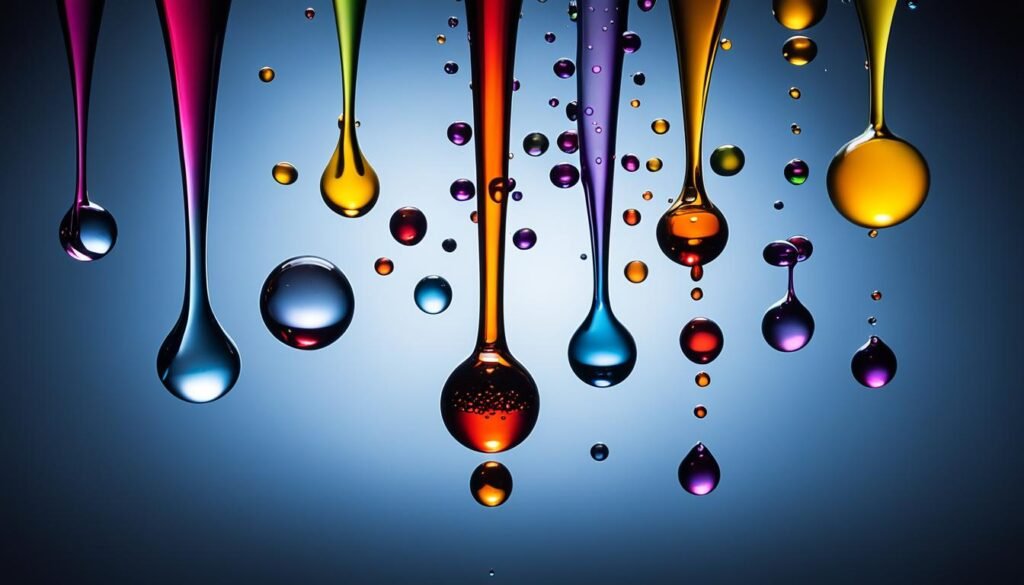
“The right resin can make all the difference in micro-molding – it’s the foundation for achieving flawless precision and performance.”
- Understand the unique material properties needed for micro-molding
- Explore the versatility of medical-grade plastics and specialized resins
- Use THY Precision’s expertise to improve the injection moulding process
Automating for Precision and Consistency
THY Precision is a top name in medical injection moulding. They focus on automation and precision for quality control. They use the latest technologies to meet ISO 13485 standards.
They use a part aligner for precise positioning of parts. They also have Automated Optical Inspection (AOI) systems. These systems check micro-parts for quality, ensuring consistency.
- Part aligners ensure precise part positioning and alignment during the injection moulding process step by step
- Automated Optical Inspection (AOI) systems automate the quality control process for micro-parts
- These advanced technologies align with the ISO 13485 certification, ensuring the highest standards of precision manufacturing and quality control
THY Precision also has top-notch clean room facilities. These rooms are ISO Class 8 and 7, which means they’re very clean. This helps make sure their products are safe and clean.
“The combination of ISO 13485 standards and advanced clean room facilities empowers THY Precision to produce medical-grade products of the highest quality, including chamber filters, dialyzer filters, intravenous infusion drips, and bacteria filters.”
THY Precision is all about automation, precision, and quality control. They’re committed to making top-quality injection moulding process step by step solutions for the medical field.
Conclusion
The injection moulding process is key to turning raw plastic into many products, especially in the medical field. It involves steps like plasticizing and injecting molten plastic. By getting each step right, companies like THY Precision can make products just right for the medical industry.
THY Precision is all about top-notch technology, strict quality checks, and clean rooms. This makes them great at making medical-grade plastic parts. They use the injection moulding process to make sure your micro-parts are perfect for the medical industry.
The need for the injection moulding process will keep growing as technology advances. This lets companies like THY Precision make even more amazing micro-parts. By leading in this field, they help you and others innovate in medical device production.